The Evolution and Impact of 3D Printing: A Technological Revolution Unveiled
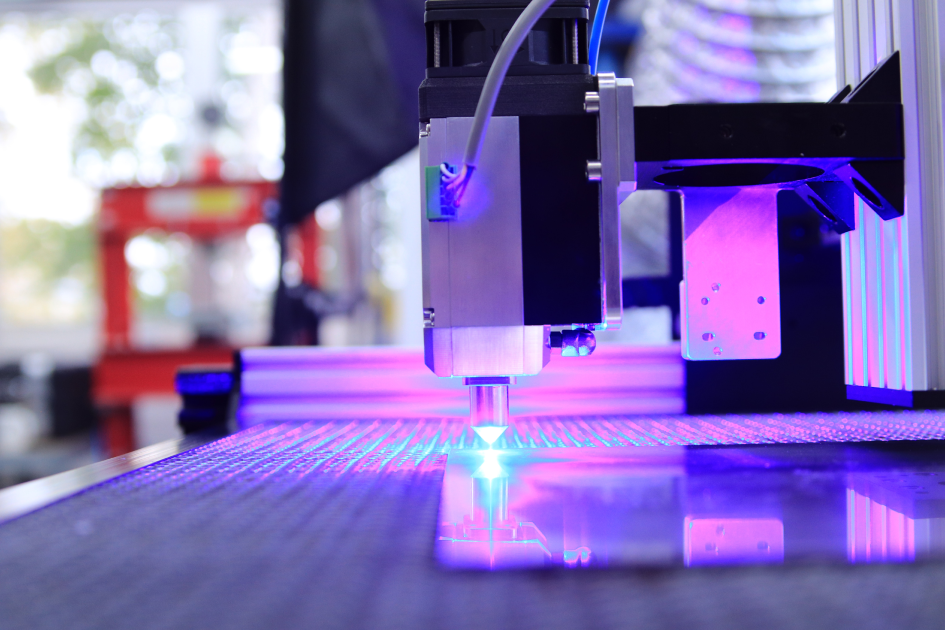
The world of manufacturing and innovation has witnessed a paradigm shift with the advent of 3D printing technology. Often referred to as additive manufacturing, 3D printing has transformed industries, enabling the creation of intricate designs, prototypes, and even fully functional products with unprecedented precision and speed. This article delves into the evolution, applications, benefits, and challenges of 3D printing, highlighting its profound impact on diverse sectors.
The Evolution of 3D Printing
3D printing traces its roots back to the 1980s when its precursor, stereolithography, was developed by Chuck Hull. The process involved creating solid objects from digital designs by adding successive layers of material. Since then, 3D printing has evolved exponentially, embracing a variety of techniques and materials, including plastics, metals, ceramics, and even biological materials.
Layer by Layer: How 3D Printing Works
At the core of 3D printing lies the principle of additive manufacturing. Unlike traditional subtractive manufacturing methods that involve cutting away material from a larger piece, 3D printing builds objects layer by layer. The process begins with a digital 3D model created using computer-aided design (CAD) software. This virtual model is then sliced into thin horizontal layers, which serve as instructions for the 3D printer. The printer deposits material, often in the form of filaments or liquid resins, layer upon layer, gradually building the physical object.
Applications Across Industries
The versatility of 3D printing has propelled its adoption across a multitude of industries, redefining the way products are designed, developed, and manufactured.
- Prototyping and Design: 3D printing has revolutionized the prototyping process, allowing engineers and designers to create rapid prototypes and iterate on designs with remarkable speed. This has significantly reduced development cycles and enabled more innovative and efficient product design.
- Healthcare: The medical field has embraced 3D printing for the creation of patient-specific implants, prosthetics, and even complex organs. Surgeons can now practice on accurate 3D-printed models before performing delicate procedures, enhancing precision and patient outcomes.
- Automotive and Aerospace: The automotive and aerospace industries leverage 3D printing for lightweight and high-strength components. This technology enables the production of intricate parts that were previously unfeasible through conventional manufacturing techniques.
- Fashion and Art: Designers and artists have harnessed 3D printing to push the boundaries of creativity. From avant-garde fashion pieces to intricate sculptures, artists can materialize their visions with unprecedented intricacy.
- Consumer Goods: Customization has taken center stage in consumer goods, with 3D printing allowing personalized products ranging from smartphone cases to jewelry. This mass customization has disrupted traditional supply chains and retail models.
Benefits and Advantages
The proliferation of 3D printing is attributed to a range of benefits that it offers to various industries:
- Reduced Material Waste: Traditional manufacturing often results in substantial material wastage. 3D printing, being an additive process, significantly reduces material wastage by using only the required amount of material for each layer.
- Complex Geometries: Conventional manufacturing methods often struggle with producing intricate and complex designs. 3D printing excels in this area, enabling the fabrication of geometries that were previously unattainable.
- Speed and Efficiency: 3D printing accelerates production cycles by eliminating the need for tooling and molds. This has profound implications for industries that require rapid prototyping and iterative design processes.
- Customization and Personalization: The ability to create unique, customized products on-demand has transformed how businesses engage with consumers, offering tailor-made solutions to meet individual needs.
Challenges and Future Prospects
Despite its revolutionary potential, 3D printing faces several challenges that researchers and industry experts are actively addressing:
- Material Limitations: While 3D printing has expanded to encompass various materials, some industries require specialized materials with specific properties that are not yet fully achievable with current 3D printing technologies.
- Quality Control: Ensuring consistent quality across 3D-printed objects remains a challenge, especially for critical applications like aerospace and healthcare, where precision and reliability are paramount.
- Intellectual Property and Regulation: The ease of replicating objects through 3D printing has raised concerns about intellectual property rights and regulatory frameworks. Ensuring proper attribution and preventing unauthorized reproduction are ongoing challenges.
- Scalability: While 3D printing is excellent for producing prototypes and small batches, scaling up to mass production levels with comparable speed and cost-effectiveness remains a hurdle.
3D printing has undeniably transformed the landscape of manufacturing and design. Its ability to create complex objects with unparalleled precision, reduce material wastage, and enable customization has revolutionized industries ranging from healthcare to aerospace. As the technology continues to evolve, addressing challenges related to materials, quality control, and scalability will pave the way for a future where 3D printing plays an even more integral role in shaping our world. Whether it's advancing medical treatments, driving innovation in product design, or even facilitating space exploration, the impact of 3D printing is poised to be felt for generations to come.